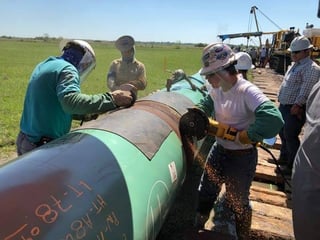
In pipeline construction, proper weld prep and interpass cleaning is crucial to the success of the overall process. Because weld failure in these applications can be disastrous, every weld must meet stringent quality requirements.
If weld defects are found, the necessary repairs add time and money to a process that typically already has a tight project timeline and may be occurring in a challenging environment.
Following best practices for weld prep beforehand and ensuring proper penetration between weld passes will help operators minimize defects and produce the high quality necessary in these demanding applications.
Choosing the Right Product
Knowing what abrasive product to use for the job is an important first step in getting the results you want. From flap discs and grinding wheels to wire brushes, there are a range of abrasive products available for pipeline weld prep and interpass cleaning. Choosing the right one helps promote high weld quality while also saving time, so welders can be more efficient. Consider these common options and their recommended uses:
- Wire brushes and wheels: Power wire brushes or wheels are a good choice for removing light surface rust or loose material on the surface of the pipe without changing the base metal. They can be used to clean the pipe surface prior to welding and for interpass weld cleaning, such as cleaning the hot pass and any subsequent passes while the weld is still hot. Brush options include stringer bead wheels and wire cup brushes (good for larger-diameter pipe and faster cleaning), as well as cup brushes, which can clean more surface material faster but require paying attention to avoid creating a kickback that can harm the material.
- Flap discs: When the pipe has more than light surface rust and has defects such as pits in the metal, a more aggressive solution will likely be needed. The bevel should always be completely cleaned and any rust or pits removed. Flap discs can efficiently grind out rust, pits and imperfections while reducing the gouging risk that comes with a grinding wheel. Flap discs are available in various material types and grit sizes, and the choice will impact aggression and material removal. For example, a flap disc with an aluminum backing is more rigid with less flex, allowing operators to maintain the edge of the bevel without rounding it, which impedes properly filling the weld.
- Grinding wheels: Grinding wheels are a good choice for grinding the root pass, facing the land and transitioning. One best practice to keep in mind with grinding wheels is to take care to avoid gouging the base material by using too much pressure. Look for a grinding wheel that is balanced to reduce chatter and provide more control. Tiger® pipeline grinding wheels from Weiler Abrasives are designed specifically for pipeline notching and grinding. They are optimized to break down and grind hot welds, which eliminates glazing, and they deliver performance right out of the box for improved efficiency. Look for a wheel like this that is specifically designed to grind hot welds without glazing.
Weld Prep and Cleaning Tips
Readying a piece of pipe for welding generally begins with preparing the bevel. Often, pipe already has a bevel created when it’s delivered to a jobsite, but it will require cleaning and shoring up the land using a grinding wheel. The land is a flat area that allows for proper spacing between the pipe ends so they can be aligned and tacked together for welding. A notching wheel or 1/4-inch grinding wheel work well for this task. Take care to avoid dwelling too long in one spot with the grinding wheel, which can gouge the base material, and keep the wheel in motion and as flat as possible when in use.
After the bevel and land have been prepared, clean the pipe opening to get it ready for welding. Wire wheels are commonly used for this task, but if the pipe has a lot of heavy rust a more aggressive product may be needed. The condition of the base material can vary a lot when it arrives on a jobsite, and the condition of the metal plays a role in choosing the right abrasive product for cleaning. A pipe with only light surface rust requires a different conditioning product than if it has heavier rust.
Interpass Cleaning
The first pass, called the root pass or bead pass, is the most critical because it creates the foundation for the remaining passes to be added on top of that bead. Once the root pass is laid, the operator must grind the weld to ensure proper penetration for the next pass, called the hot pass, to ensure full weld penetration. Using a 1/8-inch grinding wheel for this task helps create a flat or u-shape in the bottom of the weld. The hot pass must be completed quickly after the root pass to avoid the pipe temperature falling below allowable levels.
The number of passes necessary depends on pipe diameter and wall thickness, but each pass will require cleaning, typically with a knot wire brush known as a stringer bead brush. These products remove inclusions or impurities that rise to the surface of the weld without removing base material. In particular, a wire wheel with a narrow face works well for this. If the application involves larger-diameter pipes, the filler passes may have a wider v-groove, and a brush with a wider face may be a better choice. The same wire wheel used for interpass cleaning can also be used to clean the finished weld and remove any slag from the cap pass.
Wire wheels from Weiler Abrasives feature a dual-hex nut design that makes it easier to flip the wheel occasionally, which helps promote the self-sharpening ability of the wire tips. This delivers optimal cleaning action and longer life and improves safety.
Cleaning between weld passes can also be done with an encapsulated stringer bead wheel, where only the wire tips are exposed. These brushes can provide longer product life and aggressive cleaning action, but they offer the user less flexibility because of the short trim length of the wires.
6 Tips for Success
With any abrasive product used to prepare and clean pipeline welds, following some key best practices will result in safe and efficient use and optimal results. These six tips will make a difference in achieving proper weld penetration:
- Focus on proper cleaning and prep: The more thorough the weld prep and cleaning is, the fewer problems an operator will face when it’s time for weld inspection. Proper weld prep and cleaning help reduce weld inclusions and costly weld failure. Ensure that all of the pits and rust are removed from the pipe bevels just prior to the pipe being set and tacked for prep of the root pass.
- Match speed and size: The wheel or disc should fit the tool and have an rpm rating that meets or exceeds the tool’s rpm rating for safest use. Just because a product fits a specific tool does not mean it was designed to be safely used with it. Using tools and products that aren’t designed for the job introduces safety risks and can result in poor weld quality.
- Use the product as designed: Not all 1/8-inch-thick wheels are the same. Some are designed to be used vertically, while others are designed to be used for grinding as well. Always check the manufacturer’s recommendations and never use a wheel designed only for vertical use to face the land or transition pipe.
- Avoid using too much pressure: To get the most efficient and safest performance, use the proper pressure and avoid pushing too to get the product to be more aggressive. With a wire brush, excessive pressure will bend the wires so that the sides, rather than the wire tips, hit the weld. This reduces cleaning power and increases the chances of long wire breakage, increasing safety risks. Let the brush tips do the work as they are designed. With grinding wheels, pushing too hard can produce more heat, breaking down the wheel faster or causing glazing.
- Don’t notch a grinding wheel: Grinding wheels with a harder bond tend to load, which refers to base material accumulating on the wheel due to the heat of the grinding process. Some operators form chips or notches around the wheel’s edge to clean a wheel that loads, but this is a dangerous practice that can result in flying debris. Instead, look for a wheel with the appropriate bond strength for pipeline welding.
- Always store abrasive products as directed: Storing and handling abrasive products properly helps optimize their performance and extend product life. Store them in a clean, dry place and avoid laying them on the ground in wet or muddy conditions.
Ensuring full penetration in pipeline welds
Choosing the right abrasive products for pipeline weld preparation and interpass cleaning and following some key best practices can help reduce rework and improve results in these critical applications. The foundation for a high-quality weld is laid from the very beginning; taking the time for proper prep and cleaning at the start of the process can save time and money later.