Optimización del rendimiento y mejora de la eficiencia en el rectificado de rodillos
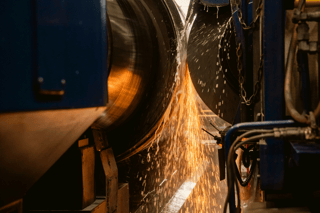
Por Kyle Thompson, Gerente del Sector de Producción Industrial de las Américas, e Inja Skrinjar, Gerente de Productos, de Weiler Abrasives
El proceso de rectificado de rodillos es fundamental en muchas industrias, ya que ayuda a mantener la precisión de las dimensiones y la integridad de los rodillos, así como la calidad de su superficie, aspectos esenciales para lograr resultados consistentes y de alta calidad en la producción.
Debido a las condiciones a menudo exigentes de este proceso, lograr el éxito en el rectificado de rodillos requiere prestar especial atención a varios factores. La alineación adecuada, la reducción de vibraciones y la selección de la rueda de rectificado correcta para el material específico de cada rodillo son factores fundamentales para producir una superficie uniforme sin ocasionar nuevas imperfecciones. Además, el mantenimiento y la inspección regulares tanto del equipo de rectificado como de los propios rodillos pueden prolongar la vida útil de la maquinaria y prevenir tiempos de inactividad costosos.
Conozca algunas de las mejores prácticas que pueden ayudar a los usuarios finales a optimizar las operaciones de rectificado de rodillos, mejorar la productividad y garantizar productos de alta calidad.
¿Qué es el rectificado de rodillos y cuándo se utiliza?
El rectificado de rodillos es un proceso de acabado de superficies que se utiliza para reacondicionar o reparar defectos superficiales, como grietas o cortes, en rodillos de trabajo grandes o de respaldo. Estos rodillos se emplean en molinos de laminación donde se forman y moldean láminas con materiales como acero, aluminio, papel y más. El proceso es común en muchas industrias, y se utiliza en fábricas de acero, bronce, cobre, aluminio y papel; plantas textiles; y en la producción de cilindros hidráulicos. Las ruedas de rectificado de rodillos se utilizan típicamente cuando los rodillos muestran signos de desgaste, como defectos superficiales o inconsistencias en su forma, y son esenciales para mantener la maquinaria funcionando de manera eficiente. Se puede utilizar en todo tipo de rodillos, ya sean fundidos o forjados, como rodillos de trabajo, rodillos de respaldo, rodillos nuevos o rodillos con uso previo que necesiten renovación.
En este proceso, se utiliza una rueda de rectificado para molinos de laminación para remover grietas o daños superficiales y restaurar los rodillos usados a su estado original o darles el acabado superficial adecuado a rodillos nuevos. El tiempo entre el rectificado o el reacondicionamiento de los rodillos depende del material que se procese. Por ejemplo, los laminadores de acero en caliente requieren más mantenimiento de sus rodillos de trabajo debido a las altas presiones y a la exposición térmica asociadas con ese proceso de laminado.
Laminado en caliente frente a laminado en frío
Cuando se procesa un metal en un molino con rectificado de rodillos, se utiliza laminado en caliente o laminado en frío en la operación. La principal diferencia entre los dos tipos de laminado radica en la temperatura a la que se procesa el metal y las propiedades que le confiere al material.
- Los rodillos de trabajo de laminado en caliente están expuestos a condiciones extremas de calor y presión, por lo que requieren rectificados frecuentes. El material es más maleable a temperaturas más altas, lo que facilita su moldeado. El laminado en caliente permite la producción de formas grandes y complejas, y reduce la necesidad de procesos adicionales. El acero laminado en caliente suele ser menos costoso de producir. Sin embargo, el acabado superficial del metal laminado en caliente suele ser rugoso y las tolerancias son menos precisas debido al proceso de enfriamiento.
- Los rodillos de trabajo de laminado en frío necesitan un reacondicionamiento constante para mantener un perfil específico del rodillo o un acabado superficial que garantice tolerancias estrictas en el producto final. En el laminado en frío, el metal se procesa a temperatura ambiente o cerca de ella. Después del laminado en caliente, el material se vuelve a procesar y se pasa por rodillos para mejorar el acabado superficial y la precisión dimensional cuando se requieren dimensiones más delgadas. El laminado en frío da como resultado un acabado superficial más liso, tolerancias más estrictas y una mayor resistencia debido al endurecimiento por deformación. Esto lo hace ideal para productos más exigentes desde el punto de vista visual y funcional.
Al elegir ruedas de rectificado para cada tipo de proceso, la principal diferencia es el tamaño del grano. Se utilizan ruedas con grano mucho más fino para el laminado en frío, ya que se requiere un acabado superficial más liso. Las ruedas para laminado en caliente suelen tener granos de tamaño 36 a 46, mientras que, en las ruedas para laminado en frío, se suelen utilizar granos de tamaño 60 a 80.
Desafíos asociados con el rectificado de rodillos
Aunque es esencial para mantener una producción de alta calidad en diversas industrias, el rectificado de rodillos implica varios desafíos que pueden afectar la precisión, la eficiencia y la vida útil tanto de los rodillos como de la maquinaria de rectificado. Estos son algunos de los desafíos habituales:
- Los distintos tipos de materiales y su composición: la variedad de materiales de los rodillos que se rectifican impacta significativamente el rendimiento de las ruedas y los costos de consumibles abrasivos para los usuarios. Los distintos materiales requieren ruedas de rectificado y técnicas específicas. La dureza y composición del material del rodillo pueden causar un desgaste excesivo de la rueda de rectificado, lo que lleva a acabados superficiales inconsistentes o a la necesidad de rectificar y reemplazar la rueda con frecuencia. Diseñar una sola rueda de rectificado que se pueda utilizar con todos los tipos de rodillos que se rectifican en una instalación determinada puede representar un desafío significativo. Busque un fabricante de ruedas que pueda ofrecer amplias capacidades, desde recursos técnicos hasta procesos de fabricación eficaces, para desarrollar soluciones que permitan lograr la calidad necesaria y, a la vez, ayuden a reducir los costos de consumibles.
- Vibraciones y marcas de ondulación: las vibraciones durante el rectificado pueden causar imperfecciones superficiales, conocidas como “marcas de ondulación”, que dan como resultado una superficie de rodillo no uniforme. Este problema puede ocurrir al trabajar con especificaciones exigentes y forzar las rectificadoras a cargas máximas para rectificar rodillos más rápido. Las marcas de ondulación no solo afectan la calidad del producto, sino que también reducen la vida útil tanto de los rodillos como del equipo de rectificado.
- Los tiempos ciclo y los costos operativos: el rendimiento de los consumibles abrasivos está directamente relacionado con los resultados financieros en la mayoría de las aplicaciones de laminado, y muchos usuarios finales buscan reducir los tiempos ciclo. A medida que la producción de un molino de laminación aumenta, las rectificadoras pueden sobrecargarse y provocar retrasos en el proceso. Si el siguiente conjunto de rodillos no está listo para un cambio, se puede producir un costoso tiempo de inactividad en la producción. Además, los rodillos en sí pueden ser bastante costosos, y a medida que se retiran capas para el reacondicionamiento, se reduce progresivamente su tamaño. Esto hace que sea importante para los usuarios finales remover la menor cantidad de material posible al renovar la superficie.
- La precisión y las tolerancias: el rectificado de rodillos puede lograr una precisión sumamente elevada y tolerancias de hasta milésimas de pulgada. Sin embargo, lograr y mantener tolerancias estrictas puede ser un desafío, especialmente para los rodillos que se utilizan en industrias que requieren alta precisión. Incluso pequeñas variaciones en la geometría de los rodillos o en el acabado de la superficie pueden provocar defectos en el producto final, lo que hace crucial mantener la precisión durante todo el proceso de rectificado.
- El desgaste y el mantenimiento de la máquina: el mantenimiento regular de los equipos de rectificado de rodillos es fundamental para prevenir problemas como desalineaciones, desgaste desigual o acabados superficiales deficientes. Mantener la precisión de máquinas grandes y complejas a lo largo del tiempo puede ser difícil y requiere operadores capacitados y un monitoreo constante.
Para abordar muchos de estos desafíos, es importante elegir una rueda de rectificado de alto rendimiento diseñada para un desempeño óptimo en cada aplicación específica. Contar con una rueda que rectifique adecuadamente y tenga una larga vida útil reducirá la cantidad de cambios de rueda y ayudará a mejorar el tiempo de actividad para el usuario final.
Productos abrasivos para el rectificado de rodillos
Al elegir la rueda adecuada para el rectificado de rodillos, considere el material y las especificaciones de la aplicación. Principalmente, se utilizan ruedas de rectificado con liga orgánica o de resina para laminado en caliente y en frío. También se utilizan algunos productos vitrificados en aplicaciones específicas en las que se requieren perfiles de rodillos especiales y acabados superficiales específicos. En las aplicaciones de laminado en caliente, se suelen utilizar abrasivos con granos de cerámica para reacondicionar los rodillos debido a la dureza del material de los rodillos y a la cantidad de material que se necesita remover. Para el laminado en frío, se utilizan abrasivos con granos de óxido de aluminio de alta calidad para mantener una tolerancia estricta en el perfil de los rodillos y aplicarles un acabado superficial específico.
El tamaño de la rueda suele estar predeterminado por el tamaño máximo que la rectificadora puede admitir. El espesor de la rueda de rectificado a veces también está limitado por las especificaciones de la rectificadora, pero se puede modificar para adaptarse a los anchos personalizados necesarios para un perfil de rodillo específico. Algunos fabricantes de ruedas ofrecen características que proporcionan flexibilidad. Weiler Abrasives, por ejemplo, puede usar una sección central económica en la rueda, que se ajusta al tamaño cuando el usuario la retira de la rectificadora al final del proceso de rectificado. Esto evita que los granos abrasivos costosos sin usar en esa sección se desechen, lo que ayuda a reducir los costos de consumibles abrasivos.
Las formas y las dimensiones de las ruedas también dependen de la aplicación. En laminado en caliente y en frío se utilizan ruedas que van desde 762 mm (30 pulgadas) hasta 1220 mm (48 pulgadas) de diámetro, con anchos de 50.8 mm (2 pulgadas) a 152.4 mm (6 pulgadas).
Otra consideración importante a la hora de elegir una rueda de rectificado es el G-ratio del producto, que mide la cantidad de material que una rueda puede remover durante su vida útil. Cuanto más alta es el G-ratio de una rueda, mayor será su retorno de inversión.
Soluciones de alto rendimiento para el rectificado de rodillos
Seleccionar abrasivos de alto rendimiento puede resultar en tasas más rápidas de remoción de material, una mayor vida útil de la rueda y menos cambios de rueda. Usar la combinación correcta de abrasivos, liga, dureza y estructura de la rueda proporciona la solución ideal para las necesidades de aplicaciones específicas. Los abrasivos de alto rendimiento permiten una mayor flexibilidad para ajustar las ruedas de rectificado y lograr el máximo rendimiento para el usuario final.
Las soluciones de ruedas de rectificado de Weiler Abrasives pueden abordar muchos de los desafíos del rectificado de rodillos, incluyendo los relacionados con vibraciones y marcas de ondulación. Las tecnologías innovadoras de formulación de ruedas y ligas le permiten a Weiler diseñar fórmulas de ruedas de rectificado específicas para los usuarios finales, y proporcionar ruedas que mantienen su forma y, a la vez, conserven suficiente refrigerante para evitar quemar los rodillos o cargar la cara de la rueda. Los especialistas técnicos ayudan a los usuarios finales a determinar la mejor especificación en función del tipo de material, la rectificadora y los parámetros de rectificado.
Los fabricantes de ruedas deben ser capaces de adaptarse a las variaciones y los requisitos de los usuarios finales y sus operaciones. Es fundamental ajustar las ruedas a la aplicación específica de rectificado. Busque un fabricante de ruedas que pueda desarrollar una matriz de ruedas adecuada para la rectificadora o los tipos de material específicos que deba rectificar.
Además, cada laminador cuenta con equipos únicos para el manejo de ruedas o con operaciones específicas de montaje de ruedas. Es importante trabajar con un fabricante de ruedas que pueda diseñar métodos específicos de embalaje que remueven los pasos adicionales con los que los usuarios finales podrían estar lidiando. Esto puede ayudar a garantizar la seguridad y rapidez en el montaje de nuevas ruedas de rectificado para los usuarios finales. Por ejemplo, Weiler Abrasives ha creado muescas en ambos lados de las ruedas para que se puedan adaptar a las bridas o a las condiciones de montaje específicas de los usuarios finales.
Además, las empresas pueden asociarse con Weiler Abrasives para disponer de conocimientos técnicos y soporte en sitio, con el fin de optimizar el rendimiento de las ruedas de rectificado y la capacidad de las máquinas. Al utilizar el programa Weiler Process Solutions (WPS), los expertos en productos trabajan en conjunto con los usuarios finales para recopilar datos valiosos y ayudar a abordar puntos problemáticos. Analizan esa información para darles su opinión y ofrecerles mejoras en los procesos que puedan ayudarlos a reducir los costos de consumibles abrasivos y mejorar la eficiencia. Por ejemplo, la reducción de los tiempos ciclo es un factor clave que se analiza como parte del programa. El ahorro de costos va más allá del costo inicial de las ruedas. Cuanto más dura una rueda, menos cambios de rueda deben realizar los usuarios. Esto puede ahorrar entre 30 y 40 minutos en cada cambio de rueda, lo que supone ahorros significativos con el tiempo. Por ejemplo, al utilizar el programa WPS, un usuario final pudo realizar operaciones de rectificado por más tiempo utilizando ruedas de alto rendimiento. Utilizó 15 ruedas de rectificado menos al año, lo que se tradujo en un ahorro de €21,000.
La capacidad de medir y rastrear las vibraciones durante el proceso de rectificado también es importante. Las vibraciones durante el rectificado pueden provocarse por muchos factores distintos, y representan un problema que puede dañar los rodillos mismos o el producto terminado y reducir la vida útil de la rueda de rectificado. Contar con experiencia técnica, además de elegir productos de alto rendimiento, puede ayudar a los usuarios finales a corregir problemas relacionados con vibraciones.
Por último, es fundamental realizar ajustes para mejorar el proceso de rectificado. Cada rueda de diferentes fabricantes funciona de manera distinta, por lo que debe asegurarse de monitorear y analizar el rendimiento y trabajar con especialistas técnicos para mejorar continuamente el proceso, en lugar de limitarse a los parámetros iniciales establecidos en la máquina. Por supuesto, también es esencial cumplir con todos los requisitos de seguridad, eligiendo productos que cumplan o superen las normas EN 12413 y ANSI B7.1.
Optimización del rectificado de rodillos
Debido a que el rectificado de rodillos es un proceso crítico en muchas industrias, es importante elegir las soluciones adecuadas que puedan ayudar a proporcionar tasas más rápidas de remoción de material, una mayor vida útil de la rueda y menos cambios de rueda. Busque ruedas de rectificado diseñadas para los requisitos de precisión y las demandas de integridad de la superficie de los rodillos en el rectificado. Esto puede ayudar a los usuarios finales a mejorar los acabados, reducir los costos de producción y aumentar la productividad.